|
Researchers
Abstract
Introduction
Materials And Methods
Results And Discussions
Conclusions
Acknowledgments
References |
Faten Alsakr1, Toufik Fayad2, Rami Alabdeh3.
1 ,2, 3Department of Geotechnical Engineering, College of Civil Engineering, Tishreen University, SYRIA
1 fatenalsakr@tishreen.edu.sy
2 tawfikabdoallahfiad@tishreen.edu.sy
3 ramihashimalabda@tishreen.edu.sy
|
|
UP |
|
Abstract
The main objective of this study is to investigate the effects of permeation grouting with (CKD) grouts on the shear behavior of costal sandy soil. A laboratory grouting model was fabricated so that the grouting process in the laboratory simulates the grouting process in the field. The studied sand was grouted with suspensions consisting of various (CKD) percentages (2, 4, 6, 8, 10, and 12%) as a proportion of the dry weight of the treated soil, and different mixing ratios (Water: CKD) (2:1, 4:1, 6:1, 8:1, and 10:1), the grouted samples were kept for curing periods of 7 days and 28 days. Direct shear tests were conducted before and after grouting to investigate the variation of shear strength and shear parameters by grouting the natural sand with (CKD) at various proportion. The results of the various investigations have proved that the values of shear strength and shear strength parameters (C, Ø) of grouted sand improved with the increase in (CKD) content and curing period in comparison to the natural sand, when (CKD) content increased from 2% to 12% the cohesion (C) of the grouted samples increased by 12.8–98.8 times respectively, while the angle of internal friction (Ø) increased by 1.02-1.21 times respectively. The values of internal friction angle (Ø) increase with the increase in (CKD) content, curing period, and (Water: CKD) ratio. The (Water: CKD) ratio has an essential effect, for each (CKD) percentage there is an optimum (Water: CKD) ratio, where the maximum values of shear strength and cohesion (C) are corresponding to that optimum ratio. Consequently, (CKD) is an efficient grouting material and can be adopted as a proper alternative to conventional grouting materials for enhancing the shear behavior of costal sandy soil. Furthermore, the use of (CKD) results in environmental, economic, and health benefits.
Keywords: by- products, permeation grouting, sand, direct shear test, shear strength parameters, curing period.
|
|
UP |
|
Introduction
Soil improvement techniques are used to modify the geotechnical properties of weak soils. Grouting is one of the techniques widely used in various fields of civil engineering. The main concept of grouting is to pump grouting materials in the form of different viscosity fluids under pressure into the rock fissures or into the soil through small diameter tubes, thereby the geotechnical performance of the treated medium is improved. The types of grouting are: permeation grouting, compaction grouting, jet grouting, and hydraulic fracturing. Grouting materials can be classified into two main categories: suspensions and solutions. Permeation grouting is a suitable method to improve the mechanical properties and bearing capacity of granular soil (Akbulut and Saglamer, 2002; Dayakar et al., 2012; Hirkane et al., 2014). Many scholars have concentrated on using grouting method to improve granular soils and made significant contribution on the study of grouting materials, equipment and procedure for grouting (Ganta, 2017; Khan et al., 2018; Li et al., 2020; Markou et al., 2017). Akbulut et al. (2002) studied the parameters that affect the grouting process to predict the groutability of granular soil. According to their experimental results obtained from the grouted sand samples prepared with various relative densities, they concluded that the sand particle size and maximum particle size of cement have significant influence on the successful of grouting process, and presented an alternative empirical formula to estimate the groutability of granular soils. Dayakar et al. (2012) investigated the effect of cement grouting with different ratios of (Water: Cement) in improving the bearing capacity of the sandy soil. The experimental results revealed that the increase in cement content and curing period increases load carrying capacity of the sandy soil. Santhosh Kumar et al. (2011) stated that cement grouting is an effective technique to improve the bearing capacity and reducing the settlement of loose sandy soils. Load settlement curves of the loose sand grouted with cement show considerable improvement in the bearing capacity. Also, the shear strength of the loose sandy soil steadily increases with increase in cement content and curing period. Dano et al. (2004) presented a comparison of the behavior of uncemented and grouted sands. They studied four types of sands, and reported that grouted sands present the general characteristics of cemented soils and can be considered as an intermediate material between soil and concrete, the friction angle is almost unchanged by the injection treatment. The cohesion varies between 0.1 and 0.5 MPa depending on the cement content of the grout and the relative density of the soil and increases in proportion with the cement-to-water ratio. Li et al. (2020) studied the relationship between reinforcement effect of permeation grouting and water-cement ratio and curing time, and concluded that water-cement ratio of slurry has obvious effect on grouting reinforcement effect. If cement slurry at high water-cement ratio is permeated into the sand layer, water bleeding phenomena will appear and lead to inhomogeneous performance of the grouted body. Maalej et al. (2007) studied the effect of cement grouting on strength of a granular medium, and concluded that cement grouting has caused a remarkable increase in the cohesion (C), while the increase in angle of friction is negligible with respect to cohesion.
Most of previous studies have used conventional grouting materials (cement, fine cement, cement with chemical additives, etc.). however, the use of conventional grouting materials causes additional costs.
Recently, the use of industrial waste has received widespread global attention because its accumulation poses an environmental and health hazard, besides its disposal by landfilling is expensive and demands vast areas, thus many researches have focused on utilization of industrial wastes in geotechnical engineering. One of these waste products is cement kilns dust (CKD) produced in large quantities during the manufacture of ordinary Portland cement, which threatens the health and environment, it can be utilized to improve weak soil properties. In addition, the use of (CKD) is considered an ideal solution to get rid of the increasing (CKD) quantities annually, using CKD as a grouting material would also lower the solid waste problem in cement industry. Thus eliminate its negative impacts on the environment, health, and cement industry (Adaska et al., 2008; Elbaz et al., 2019; Miller and Azad, 2000).
Sandy soil covers the Syrian coast and considered weak soil due to its poor geotechnical properties and low bearing capacity at shallow depths, which result in excessive settlements and shear failure. Eventually, that causes the failure of the whole structure. Therefore, the structures in the coastal region in Syria are often constructed on deep footings, but this traditional solution may be expensive.
The lack of research that studied the effect of (CKD) as a grouting material on the properties and strength of the grouted medium makes it necessary to expand on this topic. Therefore, this investigation was conducted to assess the influence of permeation grouting using (CKD) grouts on shear behavior of costal sandy soil.
|
|
UP |
|
Materials And Methods
Sand
The sand used in this study was obtained from the beach of Snobar Jbleh town, which is located in the south-east of Latakia city; (13 km) from the city center. Standard laboratory tests were used to obtain its properties. Physical and mechanical properties of the used sand are listed in "Table.1". The sand is classified as poorly graded sand (SP) according to USCS, all tests were performed in accordance with American Society for Testing Materials (ASTM) Specifications. The grain size distribution curve of sand is illustrated in "Fig.1".
Cement Kiln Dust (CKD)
Cement kiln dust (CKD) is an available material in Syria due to widespread cement manufacturing, (CKD) was obtained from cement factory of Tartous. The chemical analysis results are listed in "Table.2", the physical and mechanical properties of the used (CKD) are: Specific gravity (3.1). Blaine's specific surface (3330cm2/g). Initial setting time (196min). Final setting time (287min). Compressive strength (34N/mm2) after7 days. Compressive strength (41N/mm2) (28 days), tests were done in Tartous cement factory Laboratory. The grain size distribution curve of (CKD) is illustrated in "Fig.1".
Grouting Process
Permeation grouting process was performed as follows; using a laboratory grouting model shown in "Fig. 2": First of all, the sand was dried for (24 hours) by an oven at (105o C) before conducting grouting. Next, a metal frame was placed at the top of the box to maintain the place of the pipes and their vertical position. Then, the dried sand was filled in the box; the sand bed was prepared at the loosest state by pouring the dried sand through a funnel placed at the top of the box. After that, the suspension consisting of ((CKD) and clean tap water) was prepared in the mixing container, it was well mixed for 10-15 minutes before grouting, the mixing continued during the grouting process to get a uniform suspension and to avoid separation of water from (CKD). Then, the suspension was pumped under pressure into the four pipes uniformly, the grouting pressure was (1.5 - 2) bar and the pressure gauge was used to measure the grouting pressure, so the suspension was flowed and placed within the pores of the sand bed. Finally, after the grouting process was completed, the four pipes were pulled quietly and carefully, filling their place with dry sand.
The sand bed was grouted with a suspension consisting of different percentages of (CKD) (2,4,6,8,10, and12%) as a proportion of the dry weight of the treated sand, and different mixing ratios (Water:CKD) (W:CKD=2:1, 4:1, 6:1, 8:1, and 10:1). The procedure was repeated for each percentage of (CKD) and the different ratios of (Water:CKD). The efficiency of permeation grouting essentially depends on the penetration of the grouting material through the sand pores (Dayakar et al., 2012). "Fig.3" illustrates the penetration of (CKD) suspension into the pores of the grouted sand using Polarizing Microscope, the range of magnification is 40x.
Direct Shear Tests
A series of direct shear tests were conducted before and after grouting; to verify the feasibility of utilizing (CKD) to improve the shear behavior of the studied soil. Directly after the implementation of grouting process, the shear samples were extracted from the grouted sand bed; by inserting circular plastic molds with the same diameter and height of the standard circular shear mold as shown in "Fig.4", the extracted samples were kept in the laboratory for curing. Direct shear tests were carried out on the soil samples before grouting to determine the shear strength and shear strength parameters of the untreated sand, and after grouting to determine the shear strength and shear strength parameters of the grouted sand after (7-28) days of curing. Direct shear tests were carried out in accordance with the procedure given in ASTM D 3080-1998, using a full digital and computational control direct shear apparatus. The shear was applied at a constant rate of 5mm/ min. Three specimens were tested to obtain the values for each studied case, the procedure was repeated on the three specimens, each subjected to different vertical loads, the normal stresses applied were: (100, 200 and 300) kPa.
|
|
UP |
|
Results And Discussions
Firstly, direct shear tests for the natural sand were performed. Then, direct shear tests were done for the grouted sand for all cases after (7&28) days of curing. During the direct shear test, the magnitudes of shear forces, horizontal deformations and vertical deformations are recorded simultaneously. The normal stress and shear stress were obtained by dividing the normal force and the shear force by the area of the sample. The shear stress versus horizontal displacement curves were plotted, for natural sand and grouted sand, from which the values of maximum shear stress at failure were obtained in each case. By means of direct shear tests; shear strength parameters (cohesion (C) and the internal friction angle (Ø) for each case) were defined according to Mohr- Coulomb's failure criteria; from the relation between maximum shear stress versus normal stress from the best fit straight line through three points resulting from three tests. From "Fig.5(a)" it is shown that in the case of natural sand, the horizontal displacements increase with the increase of shear stresses until shear failure occurs, where shear failure occurs at a high value of horizontal displacements. From "Fig.5(b)" for the grouted sand with (CKD=12%) at the optimum ratio (Water/CKD=2) after (28) days of curing, it can be noted that for high (CKD) content, shear failure occurs at a low value of deformations and the peak of stresses (at failure) increases and becomes clearer. It can also be noted that the (shear stress- shear deformation) relation is almost linear relation prior the peak. the difference in trend of stress-deformations relation for natural sand compared to grouted sand can be attributed to the hardness and cohesion that the grouting material gives to the treated sand. therefore, the failure modes of the grouted samples are brittle failure and with the increase of (CKD) content the brittleness increases. "Fig.6" shows the effect of (W/CKD=2) and (CKD=12%) on shear strength at different normal stresses after (7 & 28) days of curing. The effect of (CKD) content and (W/CKD) ratio on cohesion (C) and internal friction angle (Ø) of grouted sand after (28) days of curing are shown in "Figs.7-8". From "Fig. 6(a)", "Fig. 7(a)", and "Fig. 8(a)" it can be noted that the values of shear strength and shear strength parameters (C&Ø) of grouted sand increase as (CKD) content increases, this is due to the chemical reaction between (CaO) and (SiO2) and water, this chemical reaction results in a bonding material, Calcium Silicate Hydrate (C-S-H), which binds soil particles, so the more (CKD) content the stronger bonding material (Maslehuddin et al., 2008; Miller and Azad 2000). Also, from the results of this experimental study, it has been concluded that the values of shear strength and shear strength parameters (C&Ø) of the grouted sand increase with the increase in curing period, this can be explained by the completeness of the chemical reaction, where (CKD) is similar to cement; it needs a period of time to complete the chemical reaction process and produce a cementation material (Markou and Droudakis, 2013; Maslehuddin et al., 2009).
"Fig.6 (b)" shows the effect of (W:CKD) ratio of the grout on shear strength at different normal stresses of 100, 200, 300 kN/m2 and grouted with (CKD=12%) after (7&28) days of curing, it can be noted that the maximum values of shear strength when (CKD=12%) are at (W/CKD=2), then the shear strength values decrease with the increase in (W:CKD) ratios. The value of shear strength for each (CKD) percentage and for each (W:CKD) ratio were studied, and it has been concluded that for each (CKD) percentage there is an optimum (W:CKD) ratio results in the maximum value of shear strength. The optimum (W/CKD) ratio which leads to the maximum shear strength for each case is listed in "Table.3".
Fig. 7(b)" shows the effect of (W:CKD) ratios of the grout on cohesion (C) of grouted sand after (28) days of curing. From the relation between (Water: CKD) ratio and cohesion (C) showed in "Fig. 7(b)", it can be noted that:
- The cohesion (C) varies with (W:CKD) ratio, it is rising up to a certain limit of (W:CKD) ratio, which is the maximum value of cohesion (C) and corresponding to the optimum (W/CKD) ratio for each case. For example: for a constant (CKD) content (8%) the increase in cohesion is up to (W/CKD=4) and beyond that a reduction in cohesion is noted with the increase in (W/CKD) ratio.
- The maximum value of cohesion at the corresponding optimum (Water: CKD) ratio for each studied case was obtained and listed in "Table.4". Hence, the results of direct shear tests showed that for each (CKD) percentage there is an optimum (Water: CKD) ratio, at which the values of shear strength and cohesion (C) are maximum, this is due to the fact that the suspension has an optimum viscosity at the optimum (Water: CKD) ratio, that results in the best spread and distribution of grouting suspension and leads to the best values of the studied properties. When the (Water: CKD) ratio exceeds the optimum ratio; the suspension becomes fluid, and the concentration of (CKD) is reduced because of the bleeding caused by the surplus quantity of water (Dano et al., 2004; Markou and Droudakis, 2013), that leads to weak bonds between sand particles and reduction in the values of shear strength and cohesion (C). On the other hand, when the (Water: CKD) ratio is low, the suspension is highly concentrated and therefore has high viscosity and less penetration ability (Akbulut et al., 2002; Markou and Droudakis, 2013). The internal friction angle was determined for natural sand, then for grouted sand, from "Fig.8" it can be seen that the values of internal friction angle (Ø) increase with the increase of (W:CKD) ratio, (CKD) content, and curing period. The extent of improvement in the values of internal fraction angle (Ø) is low when compared to the extent of improvement in the values of shear strength and the cohesion (C) of the grouted sandy soil. The results of this study are in accordance with the results of previous studies (Dano et al. 2004; Maalej et al. 2007), where they reported that cement grouts improve the shear behavior of the sandy soils, so the cementation effect of (CKD) is similar to that of Portland cement, in addition to an important advantage of (CKD) which is (CKD) particles are smaller than Portland cement particles. Thus, the diffusion ability of (CKD) suspension into the sand is better than that of Portland cement suspension. Hence (CKD) grouts can be injected in formations with small voids as fine-grained sands where Portland cement grouts cannot penetrate.
|
|
UP |
|
Conclusions
Based on this experimental investigation and tests results, the following conclusion are made.
The values of shear strength and cohesion (C) of grouted sand significantly increase as (CKD) content increases.
The values of shear strength and cohesion (C) increase with longer curing period. The (Water: CKD) ratio has an essential effect, for each (CKD) percentage there is an optimum (Water: CKD) ratio, where the maximum values of shear strength and cohesion (C) are corresponding to that optimum ratio, beyond the optimum ratio there is a clear reduction in the values of shear strength and cohesion (C), the effect of (Water: CKD) ratio is more when (CKD) content is more.
The values of internal friction angle (Ø) increase as (CKD) content, (water: CKD) ratio, and curing period increase.
With the increase in (CKD) content, the (shear stress- shear deformations) relation is almost liner prior the peak, shear failure occurs at a low value of deformations and the peak of stresses (at failure) increases and becomes clearer.
The results of this study are limited to the type of sand that has been treated. Therefore, we recommend further research to investigate the effect of (CKD) grouts on sandy soils with different classification.
|
|
UP |
|
Acknowledgments
Special thanks to Tishreen University for supporting this research work, and special thanks to the invaluable cooperation of Tartous cement factory for providing us with the required quantity of cement kiln dust and for allowing the analysis of (CKD) samples in the factory laboratory.
|
|
UP |
|
References
Adaska, W. S., & Taubert, D. H. (2008, May). Beneficial uses of cement kiln dust. In 2008 IEEE Cement Industry Technical Conference Record (210-228). IEEE.
Akbulut, S., & Saglamer, A. (2002). Estimating the groutability of granular soils: a new approach. Tunnelling and underground space technology, 17(4), 371-380.
American Society for Testing and Materials, ASTM Standard C33, 2015, Volume 04.08 Soil and Rock (I); D420-D5876.
Dano, C., Hicher, P. Y., & Tailliez, S. (2004). Engineering properties of grouted sands. Journal of Geotechnical and Geoenvironmental engineering, 130(3), 328-338.
Dayakar, P., Raman, K. V., & Raju, K. V. B. (2012). Study on permeation grouting using cement grout in sandy soil. Journal of Mechanical and Civil Engineering, 4(4), 5-10.
Elbaz, A. A., Aboulfotoh, A. M., Dohdoh, A. M., & Wahba, A. M. (2019). Review of beneficial uses of cement kiln dust (CKD), fly ash (FA) and their mixture. J. Mater. Environ. Sci, 10(11), 1062-1073.
Ganta. S. (2017). Improvement of Bearing Capacity of Sandy Soil by Grouting. International Journal of Innovative Technology and Research,5(5), 7267-7270.
Hirkane, S. P., Gore, N. G., & Salunke, P. J. (2014). Ground improvement techniques. International Journal of Inventive Engineering and Sciences, 2(2), 11-13.
Khan, N., Khan, I., Ullah, A., Yasir, M., & Naseer, Sh. (2018) Performance Evaluation of Cement Grouting by Universal Testing Machine to Improve the Bearing Capacity of Sandy Soil. Irrigation & Drainage Systems Engineering, 7, (2).
Li, Z., Zhang, L., Chu, Y., & Zhang, Q. (2020). Research on Influence of Water-Cement Ratio on Reinforcement Effect for Permeation Grouting in Sand Layer. Advances in Materials Science and Engineering, V (2020) (1-12)
Maalej, Y., Dormieux, L., Canou, J., & Dupla, J. C. (2007). Strength of a granular medium reinforced by cement grouting. Comptes Rendus Mécanique, 335(2), 87-92.
Markou, I.N., Christodoulou, D. N., Petala, E. S., & Atmatzidis, D.K. (2017). Injectability of microfine cement grouts into limestone sands with different gradations: experimental investigation and prediction. Geotechnical and Geological Engineering, (52), 868–882.
Markou, I. N., & Droudakis, A. I. (2013). Factors affecting engineering properties of microfine cement grouted sands. Geotechnical and Geological Engineering, 31(4), 1041-1058.
Maslehuddin, M., Al-Amoudi, O. S. B., Shameem, M., Rehman, M. K., & Ibrahim, M. (2008). Usage of cement kiln dust in cement products–research review and preliminary investigations. Construction and Building Materials, 22(12), 2369-2375.
Maslehuddin, M., Al-Amoudi, O. S. B., Rahman, M. K., Ali, M. R., & Barry, M. S. (2009). Properties of cement kiln dust concrete. Construction and Building Materials, 23(6), 2357-2361.
Miller, G. A., Azad, S. (2000). Influence of soil type on stabilization with cement kiln dust. Construction and building materials, 14(2), 89-97.
Rimal, S., Poudel, R. K., Gautam, D. (2019) Experimental study on properties of natural soils treated with cement kiln dust. Case Studies in Construction Materials (10) (1-7)
Santhosh Kumar, T. G; Abraham, B. M; Sridharan, A; & Jose, B. T. (2011). Bearing Capacity Improvement of Loose Sandy Foundation Soils through Grouting. International Journal of Engineering Research and Applications (IJERA),1(3),1026-1033.
|
|
UP |
|
|
|
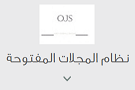 |
|
|
|
|
|
|
|
|
|
|
|
|
|
|
|
|
|
|
|
|
|
|
|
|